PRODUCTION PROCESS
First Step
Project an idea into reality.
Guide the customer towards the best and most profitable and sustainability choices in order to reduce costs and subsequently avoid delays. It is the most important phase so that in the course of development it is possible to avoid unforeseen events. Translating in a general way, we do a study on the article that the client wants to produce and we design the best way to go.
In this step, in most cases, the estimated price of the new project is delivered to the client.
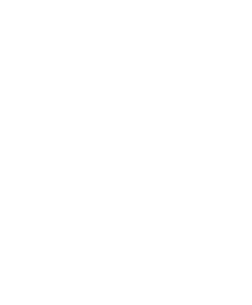
Raw material and accessories
Portugal is a country with a large number of textile companies, and we took advantage of this factor. We have a large enough network of suppliers to provide our customers with innovative solutions in their projects. Even so, we have contacts with the rest of the world for situations that we can-t find in our country, with a fast delivery times and very competitive prices.
Having traveled this path, it is up to our customer to choose the most appropriate choice for their article, always with our support to help in any doubt that may occur.
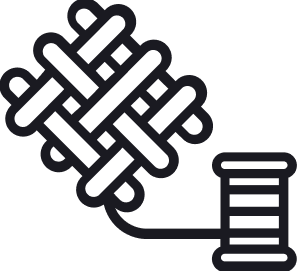
Pattern creation
Our modeling department transforms a sketch into a digital mold. This sector, being interconnected with production, is able to foresee problems and solve them in advance, reducing costs and waste of raw material.
The various pattern that we have created oblige us to have extensive knowledge in relation to this sector, such as the “waterproof jacket” has a superior technicality to the most basic models.
We are technologically updated to be able to quickly and sustainably follow market trends.
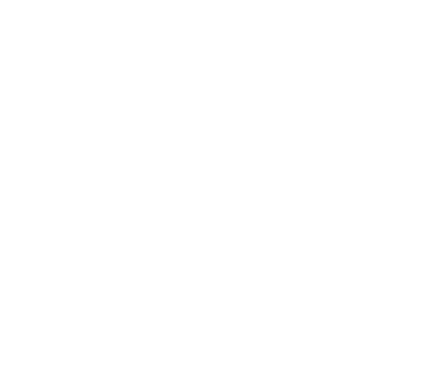
Fabric knowledge
An important area that in turn is interconnected with our modeling sector, the various existing raw materials have different behaviors between them. If we want to respect the griding table, it is necessary to record and transmit this information to the other sectors.
Various finishing processes require technical knowledge, and not all fabric compositions support different types of processes.
In a more technical area, sublimation or digital printing is usually restricted to several factors.
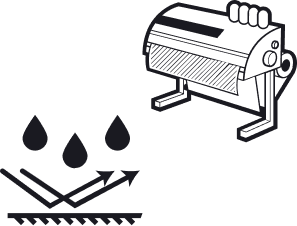
Manufacturing
With more than 40 years in the sector and the various internal technologies that we have make us a company fully capable of answer during the precess at any ocurrence while maintaining assured quality.
Starting with fully automated cutting, comprising a fabric relaxation technology to ensure that there is no shrinkage, we were able to reduce costs and increase productivity.
In production, the most diverse machines that we have available make Afortex a company with a high responsiveness, keeping the focus on the quality required of the “premium brands”.
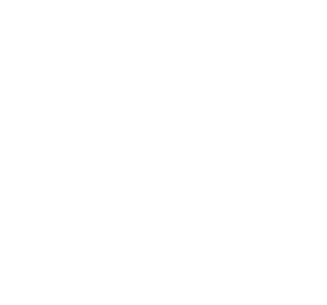
Quality control
Our quality control starts from the selection of the raw material to the packaging, always respecting the technical sheet previously prepared.
All the positions and placements of the external components of the piece are analyzed, such as embroidery, transfers, laser…, these are always accompanied prototypes to provide and get the most exact measurements possible.
Throughout the construction, several controls are carried out until the part is completed, with a final measurement being made to ensure the conformity the final product.
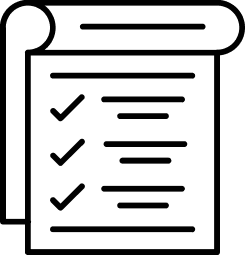
Packaging
We work with several carriers in order to guarantee the best conditions in transportation of the final product, which can be sent in various formats such as: hanging, box, pallet…
At an international level, we have answers in less than 48 hours, and for shipments by sea we have very competitive solutions.
All orders come with the proper packing list and information required by each country.
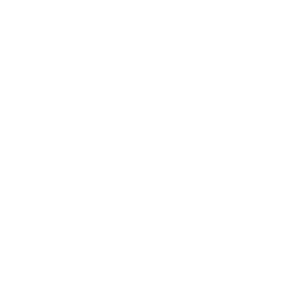